As aging multistory residential buildings in major US coastal cities face growing pressure from climate change, stricter building codes, and the demand for energy-efficient upgrades, calcium silicate board has emerged as a transformative material for modern renovations.
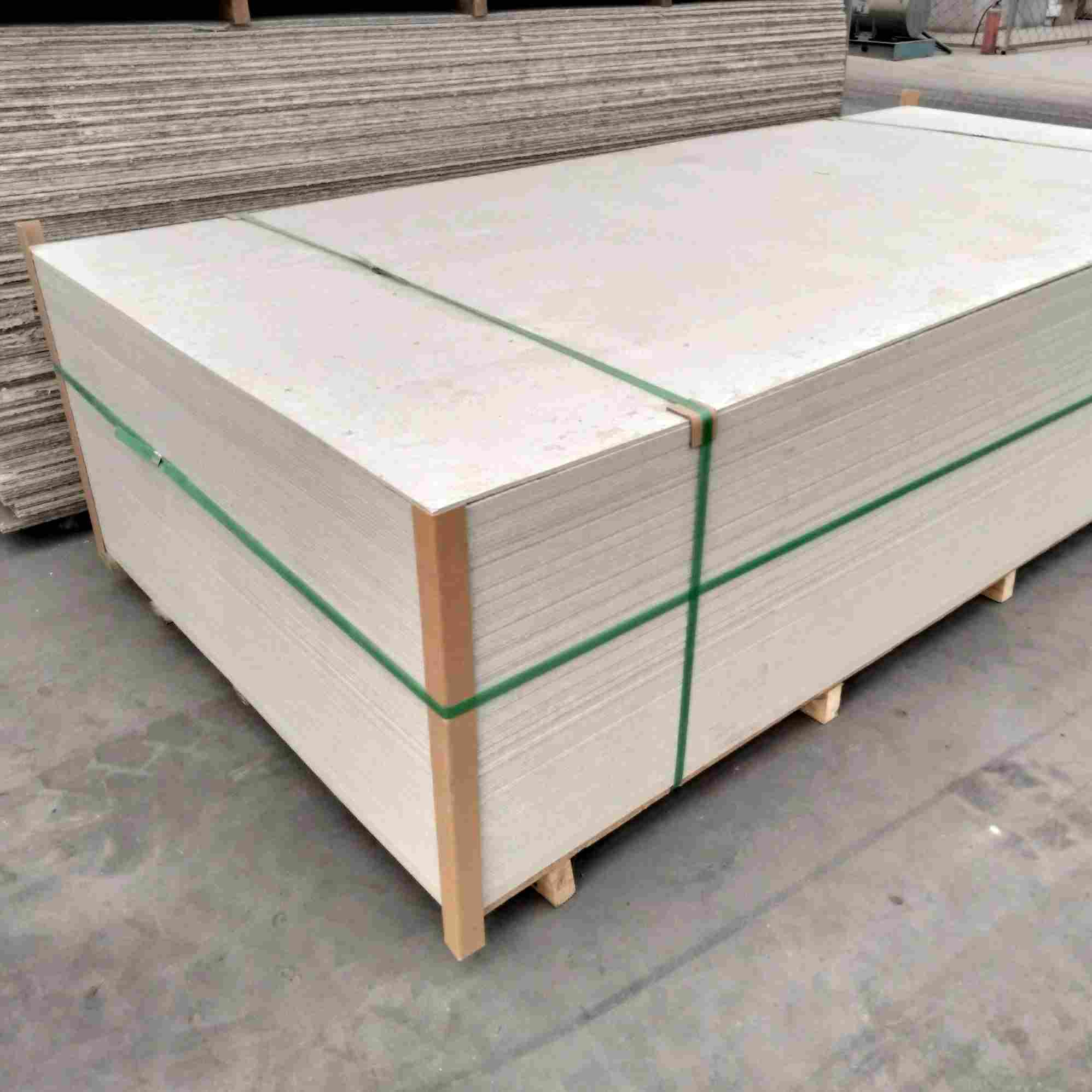
Why Calcium Silicate Board? Key Advantages for Coastal Renovations
1. Unmatched Fire Safety
Coastal cities face heightened risks of wildfires and urban blazes. Calcium silicate board, classified as non-combustible (ASTM E136), resists temperatures up to 1,200°C (2,192°F) without releasing toxic fumes. This makes it ideal for:
- Fire-rated walls and partitions: Upgrading pre-1980s buildings to meet NFPA 5000 fire codes.
- Common area cladding: Protecting stairwells, corridors, and electrical rooms in high-density housing.
2. Moisture and Mold Resistance
Coastal humidity and salt air corrode traditional materials like drywall and wood. Calcium silicate board’s non-porous structure and pH-neutral composition prevent:
- Mold growth (ASTM D3273: 0/10 rating).
- Warping, swelling, or delamination in high-moisture zones (bathrooms, basements).
3. Lightweight Durability
At 1/3 the weight of concrete but with compressive strength exceeding 15 MPa, calcium silicate board simplifies installation in aging structures without overloading load-bearing walls.
4. Design Flexibility
Available in 1/4"–1" thicknesses and 4'x8' sheets, it accommodates:
- Curved walls (via flexible variants).
- Custom textures (smooth, sandblasted, or wood-grain finishes).
- Integral color options to match historic facades.
Case Studies: Coastal Cities Leading the Charge
1. Miami, FL: Retrofitting 1960s Condominiums
- Challenge: Saltwater corrosion, hurricane-force winds, and mold infestations.
- Solution:
- Exterior cladding with 12mm calcium silicate boards for hurricane impact resistance (Miami-Dade County NOA 21-0325.04).
- Interior walls lined with fire-rated boards to compartmentalize units.
- Result: 40% reduction in annual maintenance costs; insurance premiums cut by 25%.
2. Brooklyn, NY: Revitalizing Pre-War Walkups
- Challenge: Outdated plaster walls, fire code violations, and lack of sound insulation.
- Solution:
- Overlaying existing walls with 6mm calcium silicate boards for instant fire rating upgrades (2-hour rating).
- Acoustic-grade boards in apartment partitions (STC 52 rating).
- Result: 30% faster renovation timelines; 15% higher rental yields post-renovation.
3. Seattle, WA: Earthquake-Resistant Upgrades
- Challenge: Seismic retrofitting for unreinforced masonry buildings.
- Solution:
- Calcium silicate board sheathing over brick infill walls (ICC-ES AC13).
- Lightweight panels reduced structural load by 50% compared to concrete.
- Result: Compliance with Seattle’s 2021 Mandatory Housing Affordability (MHA) retrofit requirements.
Cost-Benefit Analysis: Long-Term ROI
Metric |
Calcium Silicate Board |
Traditional Materials |
Installation Cost |
2.50–4.00/sq.ft. |
1.80–3.50/sq.ft. |
Lifespan |
50+ years (warrantied) |
15–20 years (drywall/plaster) |
Maintenance |
0.1% of initial cost/year |
2–3% of initial cost/year |
Fire Damage Repair |
$0 (non-combustible) |
50–100/sq.ft. |
Sustainability Credentials
- LEED v4.1 Compliance: Contributes to MRc2 (Building Reuse) and MRc3 (Material Reuse) credits.
- Recycled Content: Up to 75% post-consumer waste (e.g., fly ash, slag).
- Carbon Sequestration: Absorbs 0.8 kg CO2/kg during curing.
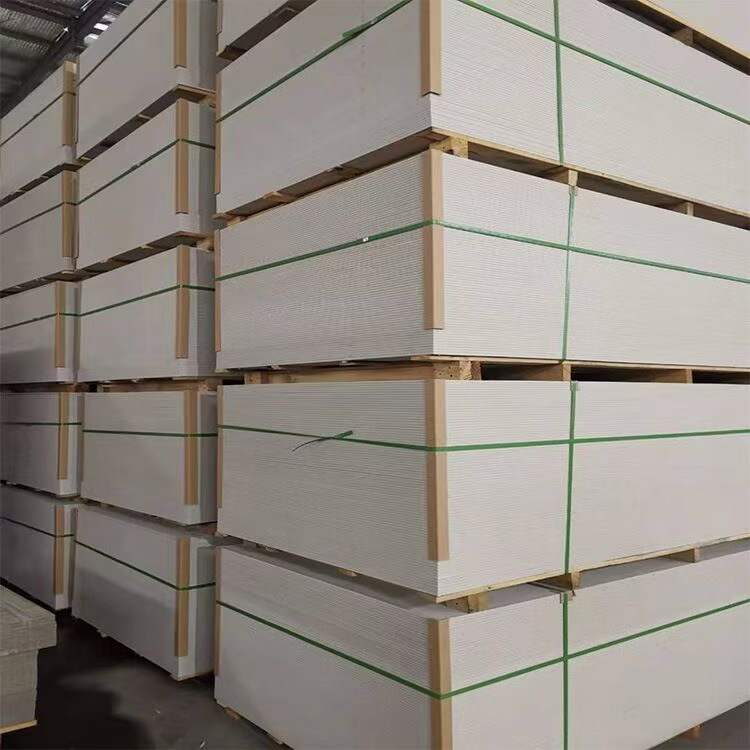
As cities like New York mandate Local Law 97 energy upgrades and Miami enforces hurricane-hardened construction standards, this material’s adaptability positions it as the go-to solution for 21st-century retrofits. For developers and property managers, the choice is clear: invest in calcium silicate board today to secure resilient, profitable assets for tomorrow.