Introduction: The Rising Demand for Ceramic Fiber Boards
Ceramic fiber boards are indispensable in industries requiring extreme heat resistance, such as metallurgy, petrochemicals, and aerospace. These boards, made from alumina-silicate fibers, offer lightweight insulation, low thermal conductivity (0.12–0.25 W/m·K), and stability up to 1,600°C (2,912°F). This guide dives into the raw materials, production steps, and quality control measures to manufacture ceramic fiber boards efficiently and safely.
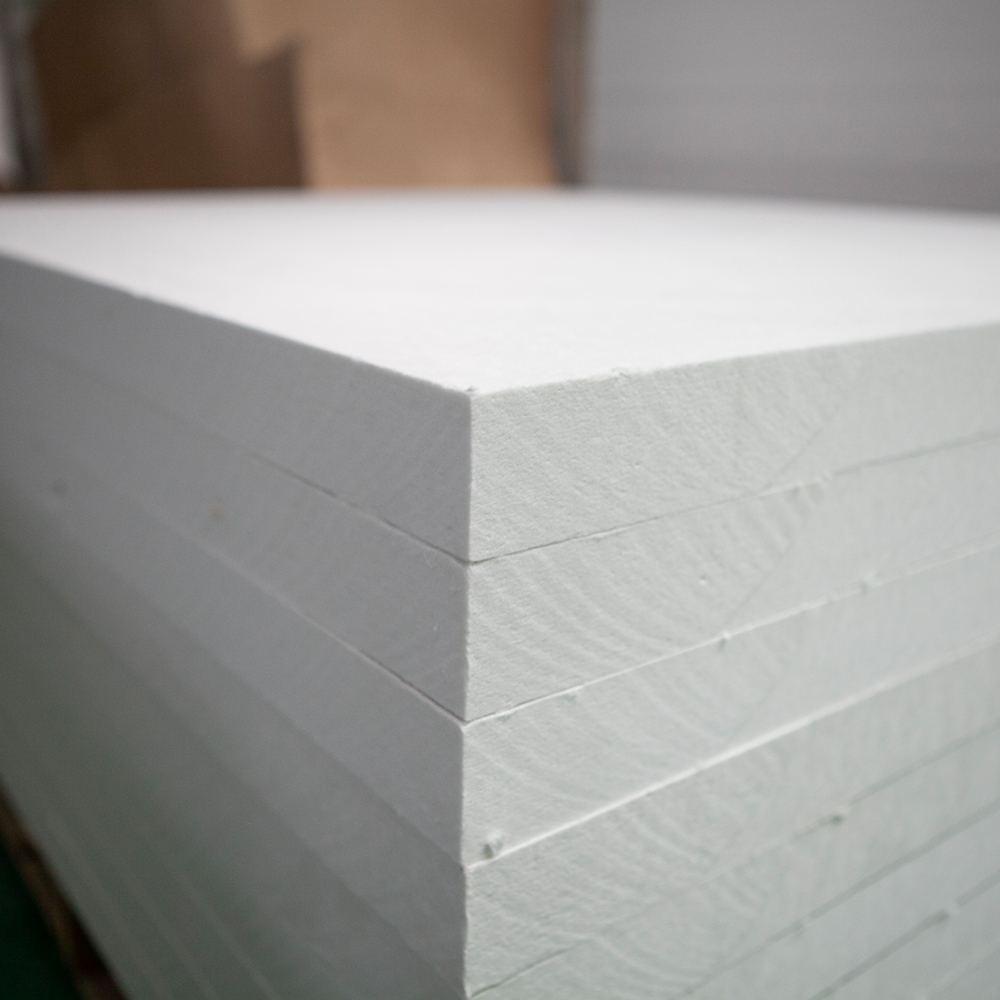
1. Raw Materials for Ceramic Fiber Boards
The production starts with high-purity ingredients:
- Alumina (Al₂O₃): 45–55% for standard boards; ≥60% for high-temperature grades.
- Silica (SiO₂): 35–45%, balances thermal stability and fiber flexibility.
Key Quality Metrics:
- Fiber Diameter: 2–4 µm (affects flexibility and insulation).
- Shot Content: ≤5% (coarse particles reduce performance).
2. Step-by-Step Manufacturing Process
Step 1: Melting and Fiberization
- Melting Furnace: Raw materials are melted at 1,600–1,800°C in an electric arc or resistance furnace.
- Fiberization: Molten material is spun into fibers using:
- Blowing Method: High-pressure air streams create short fibers.
- Spinning Method: Centrifugal force produces longer, interlocked fibers.
Step 2: Fiber Collection and Formation
- Chamber Collection: Fibers settle into a loose blanket on a conveyor.
- Vacuum Forming: Fibers are mixed with binders and vacuum-formed into sheets.
Step 3: Pressing and Drying
- Hydraulic Press: Compress the sheet to target density (260–320 kg/m³).
- Drying Oven: Remove moisture at 120–200°C to solidify the board.
Step 4: Cutting and Finishing
- CNC Cutting: Precision-cut boards into standard sizes (e.g., 1,200 × 600 mm) or custom shapes.
- Surface Coating: Optional vermiculite or aluminum foil layers for abrasion resistance.
3. Equipment Used in Production
Equipment |
Function |
Key Brands |
Electric Arc Furnace |
Melt raw materials |
Morgan Advanced Materials |
Fiberization System |
Create alumina-silicate fibers |
Unifrax, Ibiden |
Vacuum Forming Machine |
Shape fibers into boards |
Thermostech |
Hydraulic Press |
Compress boards to desired density |
Beckwood |
4. Quality Control and Testing
- Density: Measured via ASTM C167 (target: 260–320 kg/m³).
- Compressive Strength: ≥0.5 MPa (ASTM C133).
- Linear Shrinkage: ≤3% after 24h at 1,350°C (ISO 2477).
Common Defects & Solutions:
- Cracking: Adjust binder content or drying speed.
- Fiber Segregation: Optimize vacuum forming pressure.
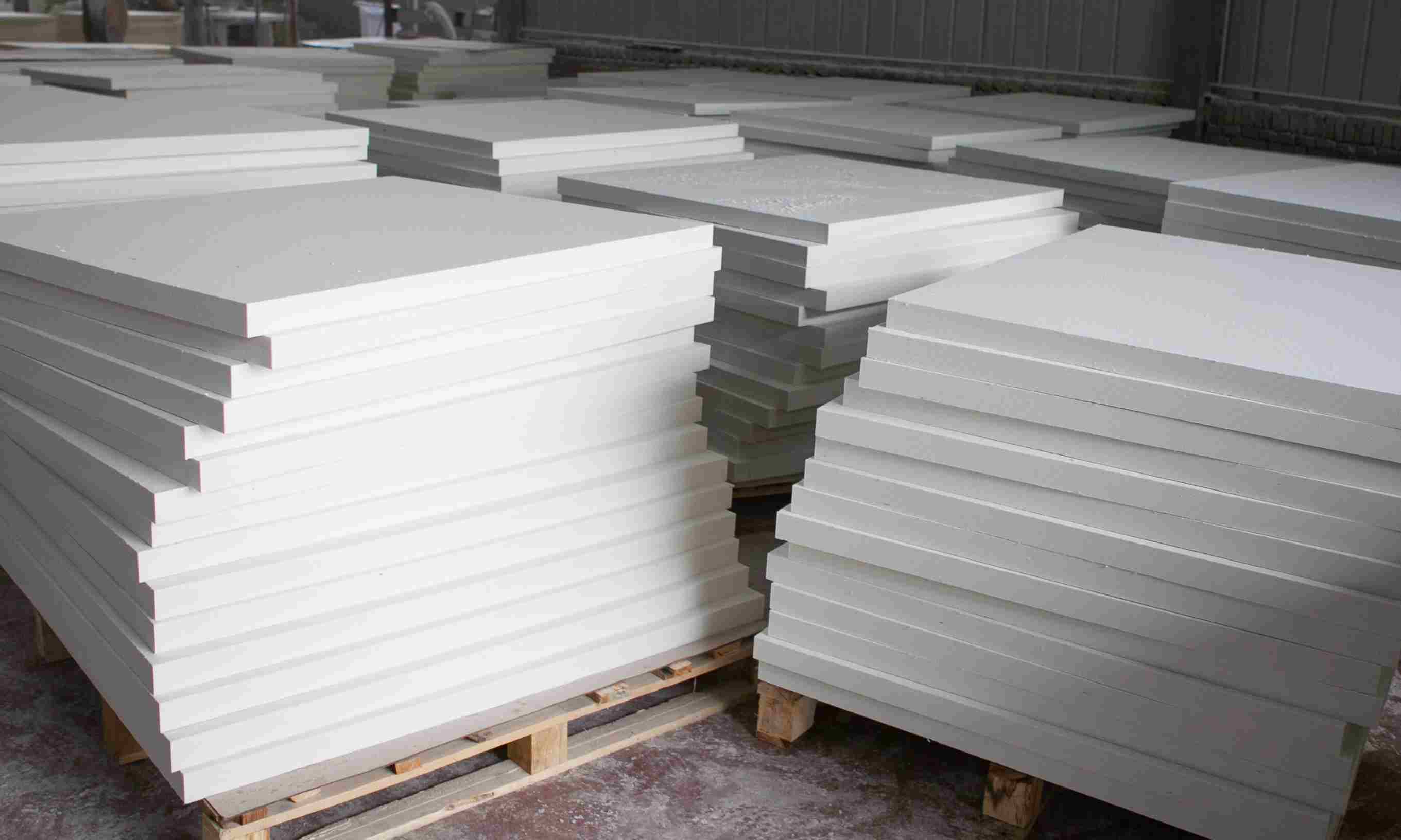
5. Safety and Environmental Considerations
- Worker Protection: Use N95 masks, goggles, and HEPA ventilation to limit fiber inhalation.
- Waste Management: Recycle off-cuts; dispose of debris per OSHA 29 CFR 1910.1001.
- Emissions Control: Scrubbers filter furnace exhaust (SO₂, NOx).
6. Applications of Ceramic Fiber Boards
- Industrial Kilns: Lining for steel reheating furnaces.
- Power Plants: Insulation for boilers and duct systems.
- Aerospace: Thermal barriers in rocket engines.
- DIY Projects: Custom insulation for home foundries.
7. FAQs About Ceramic Fiber Board Production
Q: Can I make ceramic fiber boards at home?
A: Not recommended—industrial-grade equipment and safety protocols are essential.
Q: What’s the cost to produce ceramic fiber boards?
A: Raw materials account for 50–60% of costs; a small plant requires ~$500k investment.
Q: How long does production take?
A: 3–7 days from melting to finished boards.
8. Conclusion: Partner with Experts for Optimal Results
Manufacturing ceramic fiber boards demands precision, advanced machinery, and strict quality control. For startups, collaborating with certified suppliers (e.g., Nutec or Isolite) ensures compliance and efficiency. For large-scale needs, automate processes with CNC cutting and robotic handling to boost output.